In most cases, fire resistance is generally viewed as a constraint. Unless otherwise required by the client the designer seldom builds in more fire resistance than is required by the building code or the local fire marshal. However, for general safety of an interior, fire resistance can also be viewed as a basic function. There are two basic concerns with fire resistance, the surface burning characteristics of finish. and the fire resistance of an entire assembly. There are five detailing responses for creating fire resistance.
Use Noncombustible Materials in Details A basic material is considered robe noncombustible when it meets the requirements of ASTM E136. For composite materials, the sutural base must be noncombustible and the surfacing can be no more than 1/8 in. (3.18 mm) thick with a maximum flame spread of 50 when tested in accordance with ASTM E84 or UL 723. Even if the building code does not require a portion or all of a detail to be fire-resistance-rated, consider using noncombustible materials. For example, if wood blocking is allowed, metal framing may be used instead.
Limit the Amount of Flammable Materials The simplest way to create a fire-resistant surf ace is to specify a material that that has a flame spread raring below 25 (Class A) when tested in accordance with ASTM E84. Most commercial interior finish manufacturers provide materials that bare a Class A flame spread rating. Num, consider applying a fire-retardant coating as described below.
Use Applied Fire Retardants When Required When required in a detail, applied fire retardants may take four basic forms: encasement with a fire-resistant material, spay-applied fire-resistive coatings, intumescent materials, or comings. Encasement is generally with one or more layers of gypsum wallboard used to give a steel column or beam a one-, two-, or three-hour fire resistance rating. Approved methods of doing this are given in the Building Material Directory published by Underwriters Laboratories, the Fire Resistance Design Manual published by the Gypsum Association, or other reference books. Figure 3-17 shows a typical two-hour rated steel column encased in gypsum wallboard. Spray-applied fire-resistive coatings are typically applied to structural steel framing during the construction of a building and are seldom specified by the interior designer. However, if such fireproofing is removed or damaged during interior construction, it must be patched by a qualified worker. Intumescent materials are commonly used in fire-resistive-rated doors, fire-stopping penetrations through fire-rated walls and floors, and for applied coatings. An intumescent material is one that swells and chars to form a smoke and fire barrier when exposed to heat. Intumescent materials for details may take the form of sealants, gasketing, and coatings. These are generally not specified by the interior designer but may be used in door details where a positive pressure fire-rated door assembly is required. When a door must meet the requirement of positive-pressure fire testing, it must have approved gasketing or intumescent material along its edge or on the frame. The material can be placed in a small dado along the edge of the door or in a reveal in the frame. Fire-retardant coatings may also be applied to wood panel products, finish paneling, metal, fabrics, and other materials to give then a Class A flame spread rating. However, the available colors and textures may be limited, depending on the product and manufacturer, and may affect the final, finished appearance.
Use Only Tested and Rated Assemblies and Materials Fire-resistance rated assemblies, such as partitions, doors, and glazing, need to be tested according to industry standards to be approved for use in buildings. For example, partitions and some glazing systems must meet the requirements of ASTM E119, Standard Test Methods for Fire Tests of Building Construction and Materials and doors must be tested in accordance with NFPA 252, Fire Tests of Door Assemblies. Refer to Table 2-4 for a summary of fire testing required for various interior components. The interior designer must verify with the manufacturer that a product or assembly meets the requirements of the local building code.
Use Listed or Labeled Components For individual components, such as electrical devices, lighting fixtures, doors, hardware, and other building products, an independent testing laboratory may be required to verify that the component meets the requirements of a standard. One of the best-known testing laboratories is Underwriters Laboratories (UL). When a product successfully passes the prescribed test, it is given a UL label. There are several types of UL labels, and each means something different. When a complete and total product is successfully tested, it receives a listed label. This means that the product passed the safety test and is manufactured under the UL follow-up services program. A classified label means that samples of the product were tested for certain types of uses only. In addition to the classified label, the product must also carry a statement specifying the conditions that were tested for. The detailer should verify that required products, such as electrical devices, are UL listed or labeled or that other approved testing agencies have tested the product.
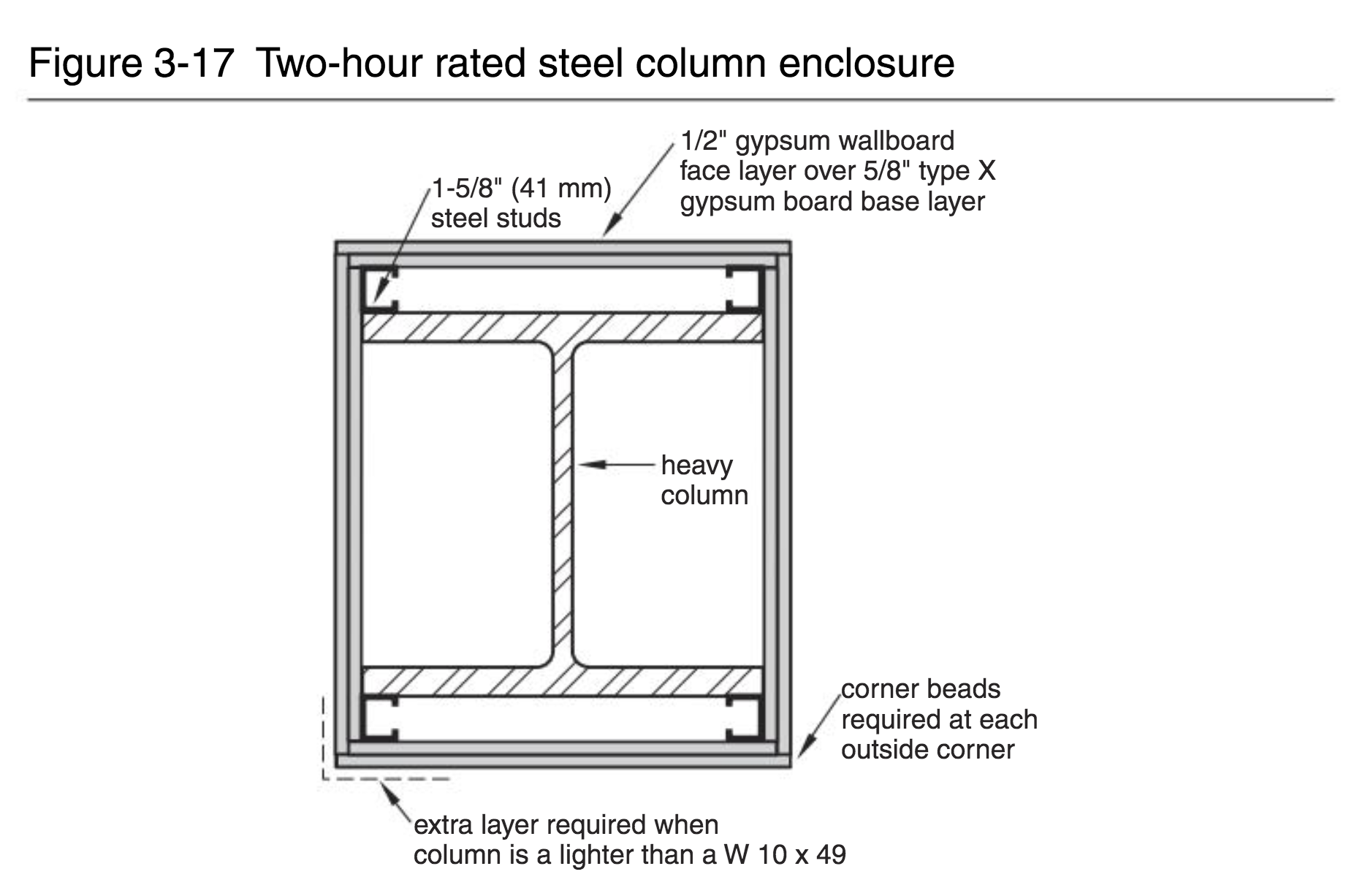